Applications of Stainless Steel in the Chemical Industry
Stainless steel, also known as inox, is one of the most essential materials in the chemical industry. With its exceptional advantages in corrosion resistance, mechanical strength, and design flexibility, stainless steel significantly contributes to improving efficiency, ensuring safety, and promoting sustainable development in this field. Let’s explore some of its key applications in the chemical industry with Sơn Hà SSP through this article!
1. The Importance of Materials in the Chemical Industry
Chemical engineering focuses on the technologies, equipment, and processes used to transform raw materials into consumer products. Therefore, the chemical industry is considered a cornerstone supporting numerous critical sectors, including pharmaceuticals, energy, agriculture, and advanced material development.
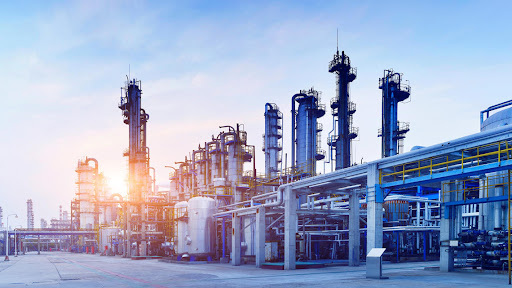
Materials play a critical role in the chemical industry
Due to their importance, the materials used to manufacture equipment and systems must meet stringent quality standards to:
- Ensure Safety: Prevent the leakage of hazardous chemicals, protecting both people and the environment.
- Maintain Performance: Ensure stable and uninterrupted operation of equipment.
- Extend Longevity: Minimize maintenance and replacement costs.
Stainless steel stands out as a material that excels in meeting all three of these requirements, particularly in harsh environments demanding durability and flexibility.
2. Stringent Material Requirements in the Chemical Industry
The chemical industry imposes exceptionally high standards for the materials used in its equipment and systems. These requirements not only ensure operational efficiency but also maintain safety in demanding working environments where corrosive chemicals, high temperatures, and significant pressures are commonplace.
Key criteria that materials must meet include:
- Exceptional Corrosion Resistance: Chemicals used in the industry, such as strong acids (sulfuric acid, hydrochloric acid), alkalis (sodium hydroxide solutions), and organic solvents, are highly corrosive. Materials must therefore exhibit outstanding resistance to corrosion. Stainless steel, particularly grade 316 with its high molybdenum content, perfectly fulfills this requirement, maintaining structural integrity and prolonging equipment lifespan.
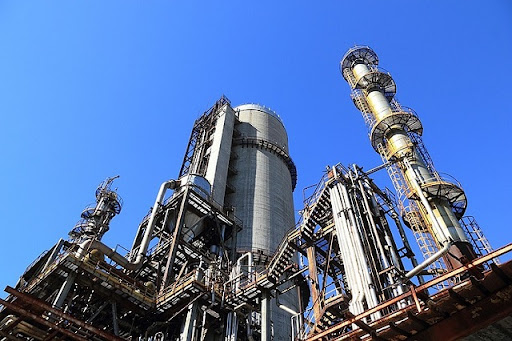
Applications of Stainless Steel in the Chemical Industry
- Superior Heat Resistance: Many chemical reactions require high temperatures, sometimes reaching thousands of degrees Celsius. The materials used in such environments must resist heat without deforming or losing their intrinsic properties.
- High Mechanical Strength: Chemical systems often operate under high pressure or extreme temperatures. This requires materials with exceptional strength and the ability to maintain stability despite significant thermal fluctuations.
Additionally, materials must meet other crucial criteria, such as being easy to clean, machinable, and flexible for diverse applications.
3. Applications of Stainless Steel in Chemical Processes and Systems
3.1. Chemical Production and Reaction Equipment
Stainless steel is widely applied in reaction equipment, which often encounters intense chemical processes. Key examples include:
- Reactors: Designed to endure high temperatures and resist chemical corrosion.
- Chemical Mixing Tanks: Ensures safety during the mixing of aggressive chemicals like nitric acid or alkalis.
- Chemical Conveyance Pipes: Safely transports chemicals between stages without leakage or corrosion.

Application of Stainless Steel in Chemical Mixing Tanks
For instance, in fertilizer production, phosphoric acid is manufactured from sulfuric acid and phosphate rock. This process requires reactors made of stainless steel to withstand the high acidity without corroding or compromising performance.
3.2. Handling and Transportation of Chemicals
Chemicals, especially hazardous or highly reactive substances, must be handled and transported under conditions of absolute safety. Stainless steel is an ideal choice due to its exceptional properties:
- Corrosion resistance: Ensures no chemical leakage occurs. .
- Smooth surface: Minimizes chemical residue buildup, making cleaning easier.
- High durability: Withstands pressure from liquid chemicals or compressed gases in storage tanks and pipelines.
A prime example is in fuel storage systems or hazardous chemicals such as acetone or chlorides, where stainless steel reduces the risk of explosions or leaks, ensuring the safety of both people and the environment.
3.3. Filtration and Separation Processes
Filtration and separation in the chemical industry, such as gas separation or crude oil filtration, demand materials that are both durable and precise. Stainless steel meets these requirements thanks to:
- Stainless steel filtration membranes: Used for filtering liquids and gases, offering high reusability.
- Heat exchangers: Made from stainless steel to enhance heat transfer efficiency and resist corrosion.
For example, in the pharmaceutical industry, stainless steel is employed in the separation of active compounds to ensure product purity and quality.
4. Conclusion
Stainless steel is not only a revolutionary material in the chemical industry but also a cornerstone for sustainable development. Its exceptional properties and broad applications make it the top choice for manufacturing industrial equipment and systems.
If you’re looking for high-quality stainless steel solutions, visit our website at https:\/\/sonhassp.com//sonhassp.com//sonhassp.com or contact us via Hotline 1800 6566 for consultation and support!